The PEM electrolyser industry relies on ultrapure flexible tubing

By 2023, this technology is expected to exceed 33% worldwide.
But this implies that all component production must now be adapted to PEM electrolyzers, considering that it is likely to be the system chosen as the most effective and efficient to produce green hydrogen.
Among the different components of the value chain to be adapted, the tubes and hoses for transporting fluids and gases stand out. There are 2 critical points to consider when talking about the pipes and hoses for the PEM electrolyzer subsystems
Tubing and hoses problems for PEM electrolyzers:
- When leaving the laboratory environment, electrolyzer producers need the hoses of the different electrolyzer subsystems to be flexible and adaptable to actual working conditions.
- One of the disadvantages or complexities of Polymer Electrolyte Membrane systems is their sensitivity to contamination. This high sensitivity means that contaminants can significantly impair the efficiency of the membrane.
Solutions for tubes and hoses in PEM electrolyzers:
- Flexibility: this first problem to solve is relatively straightforward. Flexible materials that can withstand the pressure and temperature of the different subsystems must be used. These requirements are not specific to the hydrogen industry and different types of solutions can be found.
- High purity: The real difficulty lies in finding flexible materials that contaminate the cell as little as possible, so that the efficiency of the membrane is affected as little as possible.
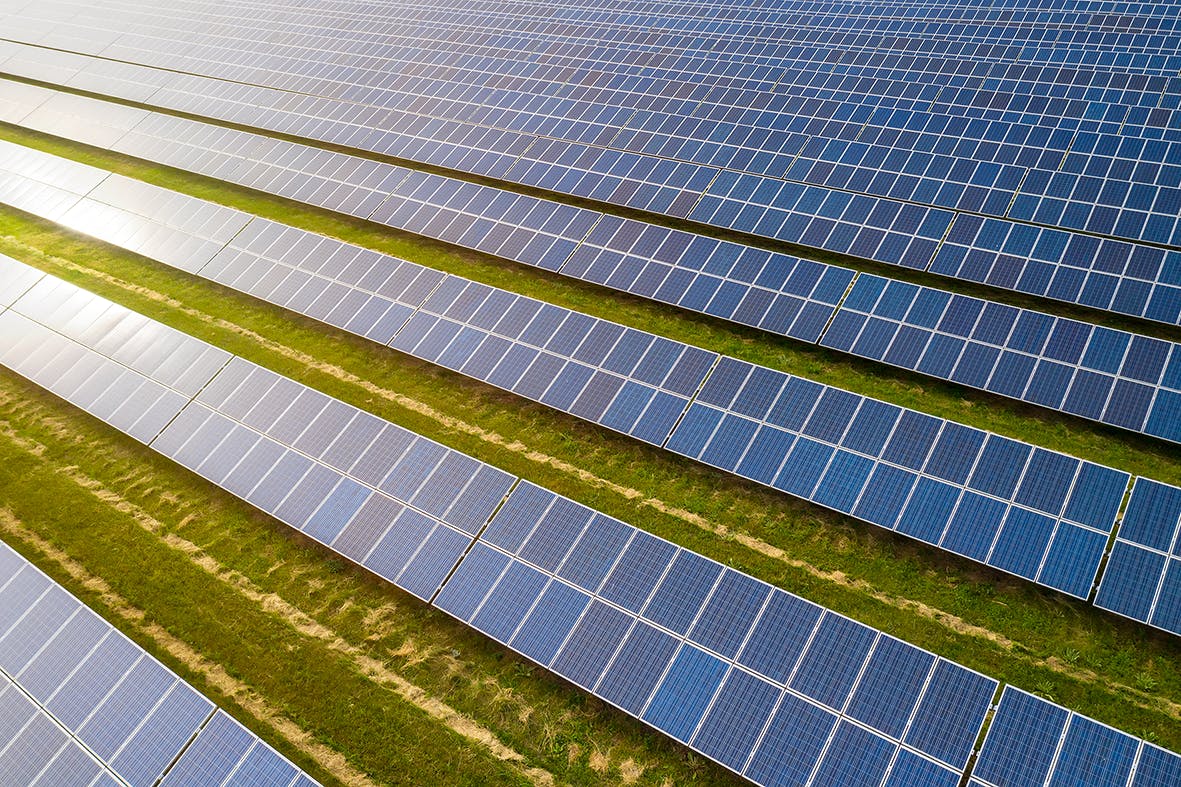
High purity in PEM electrolyzer tubes:
To get answers on this key point, we contacted Venair, which is engaged in the design and manufacture of hoses and pipes for the PEM electrolyzer industry as well as PEM Fuel Cells.
Venair has developed different flexible solutions according to the requirements of each PEM electrolyzer subsystem:
- Ultrapure Water Inlet (anode): it is necessary to maintain the maximum purity of the water in order not to contaminate the cell.
- Cathode: for the conduction of Hydrogen to its storage point.
- Cooling: for cooling the system
The high purity requirements are basically focused on the input of ultrapure water to the stack. This ultrapure water is the only external substance that enters the cell during the operation of the electrolyzer, so it is the key factor in maintaining the purity of the stack.
At Venair, the company specializes in the design, engineering and construction of flexible hoses for the PEM Fuel Cell industry, where the purity requirements are extremely similar. So with the huge growth of PEM electrolyzers, they are managing to provide a wide range of solutions for the different subsystems.
"Our company has been working for high purity industries such as BioPharma companies for many years. So, we have applied our knowledge and processes from these sectors to achieve a product for industrial use, but with a purity level that meets the standards of the BioPharma industry."
Venair's R&D department has been working for years to develop the perfect flexible solutions for the PEM technology industry. To date, they have dozens of analyses, tests and results specifically tailored to the requirements of partners working with PEM Fuel Cells and electrolyzers.