VENA® FLEXHOL Case Study
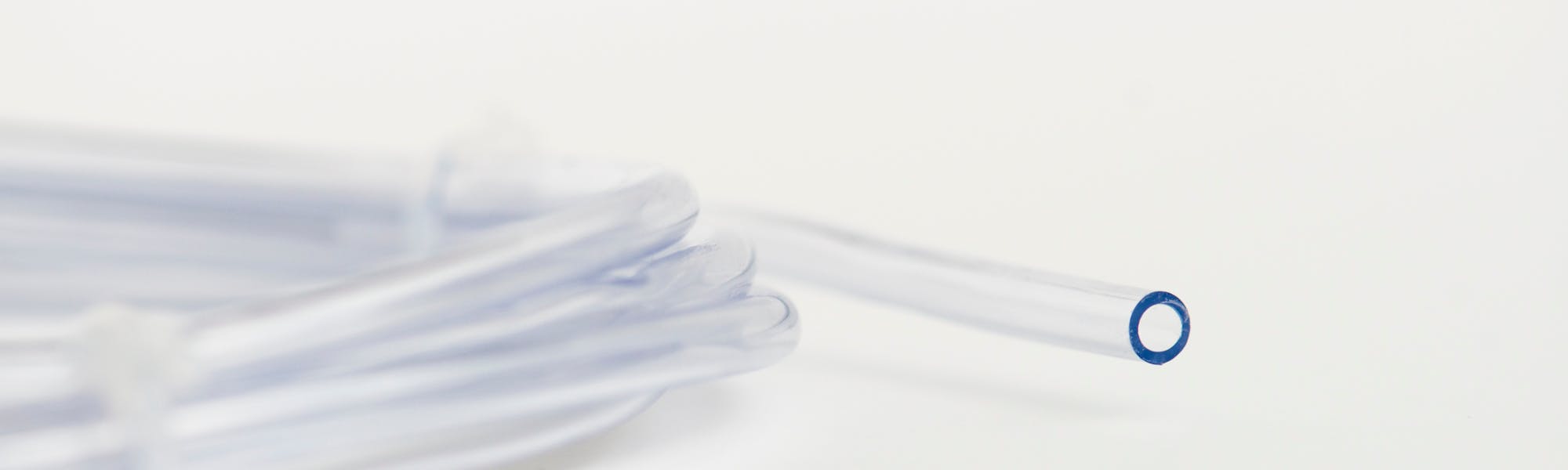
Characteristics
VENA® Flexhol is Venair’s newest extruded tubing solution. Made from food-grade materials, this tubing solution is specially catered to high-purity alcohol pump lines in various industries.
Thoughtfully tested by our R&D department, VENA® Flexhol is capable of withstanding pure ethanol and methanol pumping for hundreds of hours without failure or damage signs while providing great flexibility and translucency.
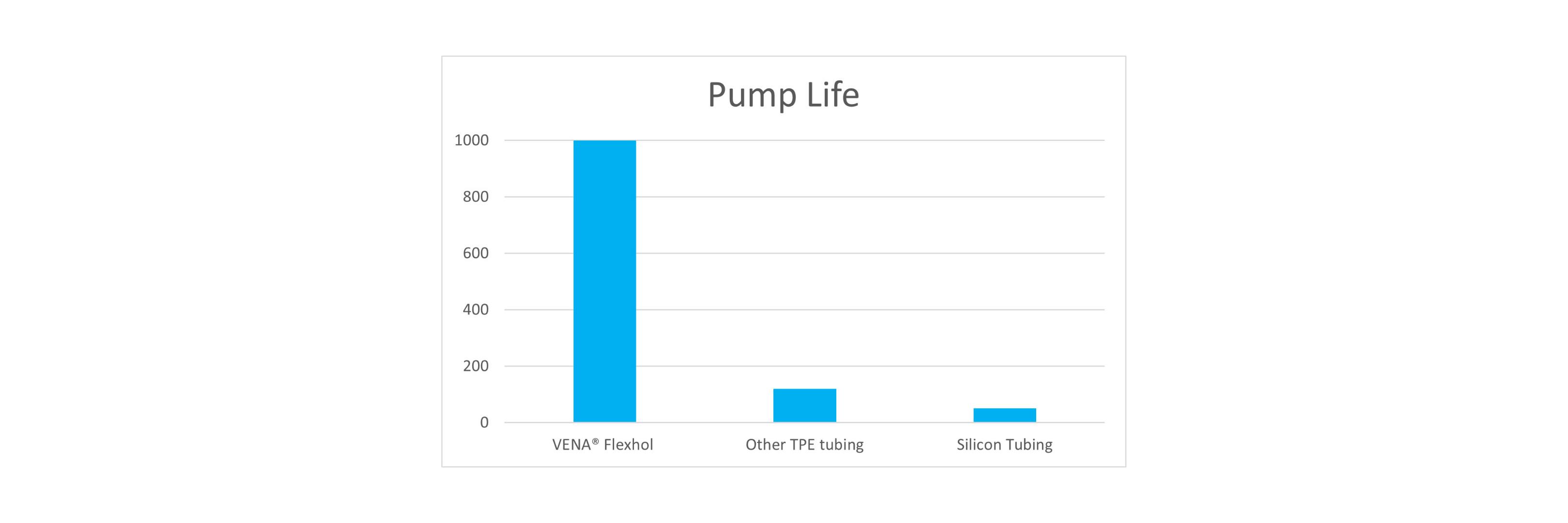
Vena® Flexhol’s real implementation
Background
The new Vena® Flexhol has been successfully implemented in a leading Spanish cosmetic company, where it has helped address some of the challenges faced in their perfume filling lines.
The company required a tubing solution that could endure extended pump cycles when transferring high-purity ethanol formulations. It was essential to maintain a high level of flexibility to seamlessly integrate the tubing into their existing lines. Effective flow control was a crucial requirement, making clear tubing indispensable. Above all, they sought a safe and non-toxic tubing option that would preserve their product's quality by avoiding odor alterations or the introduction of potentially hazardous substances.
Challenges
Until now, the company had been using standard silicon and thermoplastic tubing that was not specifically designed for transferring alcohol. This resulted in recurrent issues that they wanted to resolve through the introduction of a more suitable transfer line.
For example, the corrosive nature of the ethanol used in their perfume formulation caused a gradual deterioration of the tubes over time. As a result, the lifespan of the tube decreased, increasing the risk of leaks, and contamination, and compromising the overall quality of the final product. Additionally, the limited durability of the tubing necessitated frequent replacements, resulting in heightened downtime, elevated maintenance expenses, and disruptions in the production process.
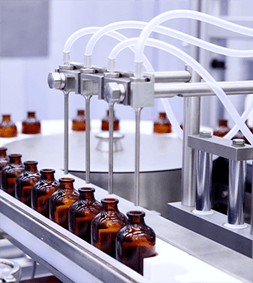
Vena® Flexhol, a suitable solution for alcohol-resistant pump lines.
By introducing Vena® Flexhol in their production processes, they ensure tubing with great chemical compatibility with ethanol that could last much longer in pump operation than previous alternatives. Besides, being completely odorless and safe for food contact, they could guarantee the quality and safety of their product while decreasing downtime and maintenance costs.
Conclusions:
The implementation of Vena® Flexhol proved to be a success for the Spanish cosmetic manufacturer. It increased productivity, reduced downtime and maintenance costs, and maintained their high-quality standards and tightly regulated process control. This is particularly crucial in an application as critical and close to the final product as perfume filling.
By offering a durable and alcohol-resistant pump solution, Vena® Flexhol establishes itself as an alternative for the cosmetic sector and other demanding industries that require highly compatible, long-lasting, and safe pump transfer lines.